Environmental Business Plan
Environmental Business Plan Overview
Our Environmental Business Plan is a unique initiative that applies business management principles to environmental conservation. We believe minimizing environmental impact is key to achieving the most efficient manufacturing globally. Since 2001, we’ve been working to reduce waste, in 2003 we expanded to reducing water consumption, and by 2021, we introduced energy efficiency-related activities.
Our goal is to continuously reduce waste and water usage through recycling and reduction, using specific intensity as a performance indicator. For energy, we focus on improving efficiency through targeted efficiency improvement plans, using energy intensity in glass manufacturing as a key metric. In line with our CO₂ emissions reduction goals, we are enhancing our electric power ratio, adopting new processes such as hydrogen combustion, and increasing our use of renewable energy.
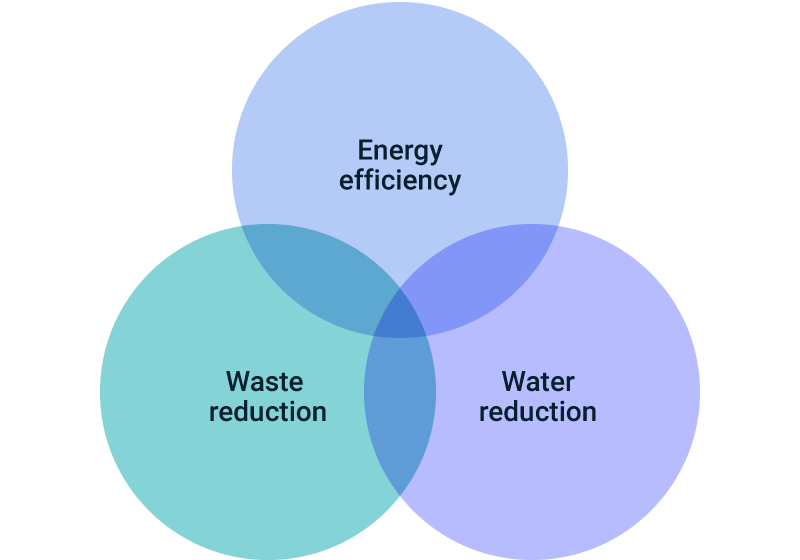
Improving Energy Usage Efficiency
In fiscal 2021, we launched an energy business plan aimed at making energy usage visible across our global manufacturing processes (melting, forming, processing) and utility facilities. The plan focuses on promoting energy efficiency and reducing wasteful energy consumption.
By analyzing the data, we identify ways to boost productivity and develop effective measures, while consistently reducing energy intensity (the ratio of production weight). Our targets and improvement plans align with our carbon neutrality action plan.
As of fiscal 2023, our energy intensity had decreased by 21% compared to fiscal 2018.
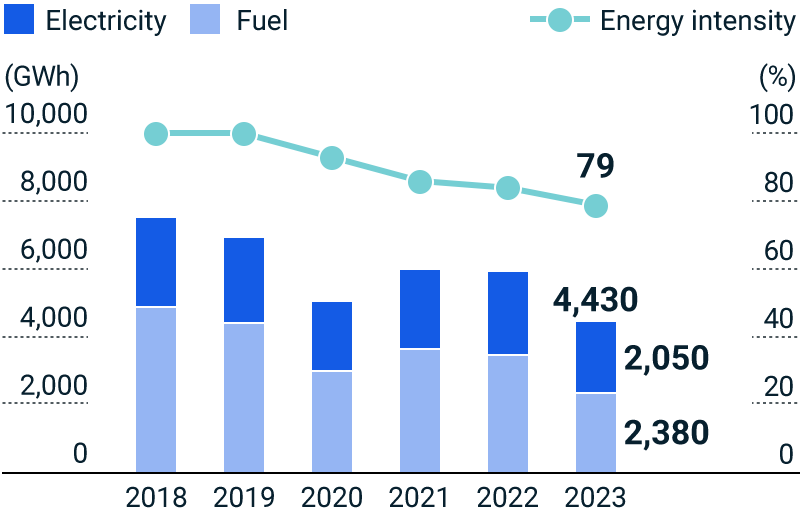
Waste Reduction
At NEG, we are committed to recycling, with a core policy of maximizing in-house recycling of all solid glass waste. Since fiscal 2001, we have focused on reducing waste as part of our Environmental Business Plan.
Waste is categorized into two groups: normal waste, generated from regular production activities, and bulky construction waste, generated from activities such as glass melting furnace maintenance.
These categories are further divided into four subcategories, with Landfill Waste D being the highest priority for reduction due to its significant environmental impact.
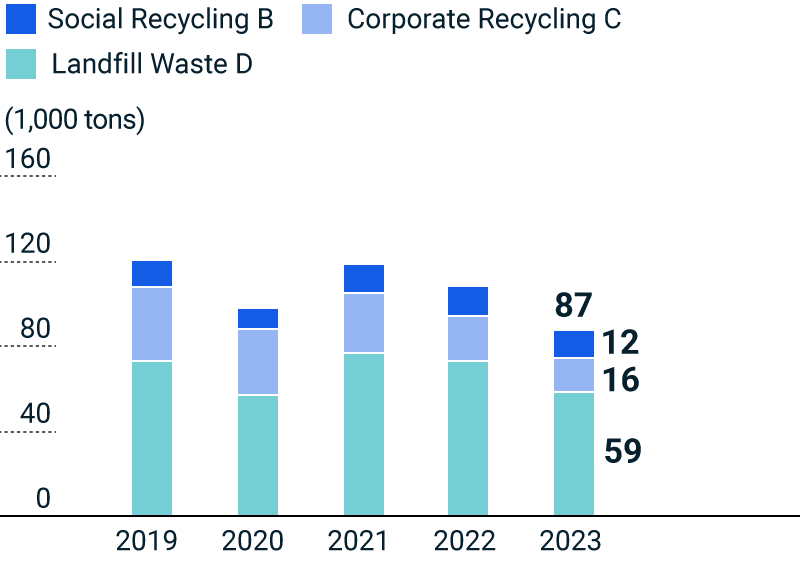
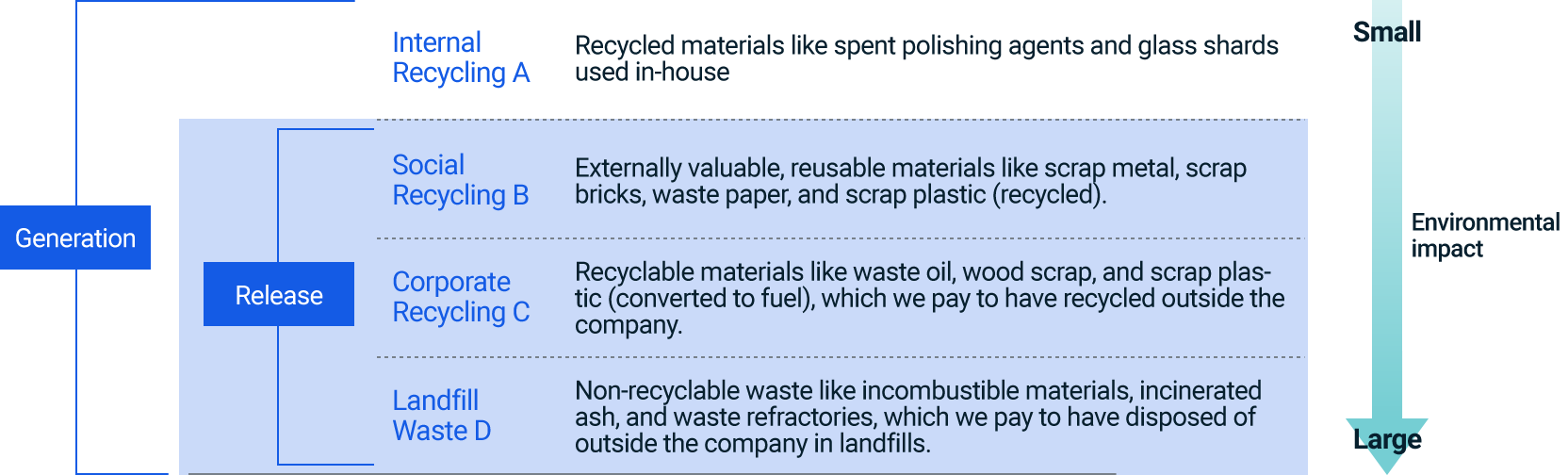
Since fiscal 2009, we’ve reduced the percentage of normal waste requiring landfill disposal (Landfill Waste D) generated from regular operations to 0.1% or less of the total weight of products sold. However, following our acquisition of composites businesses in the U.K., Netherlands, and the U.S. (fiscal 2016-2017), our overall waste output has increased. We are now working to reduce waste in our overseas operations.
Bulky construction waste, primarily non-recyclable brick from glass furnace repairs, is a major component of Landfill Waste D. Since fiscal 2017, we've shifted waste bricks to Social Recycling B by having refractory manufacturers repurpose waste chromium (Cr) and zirconium (Zr) bricks as raw materials. This has significantly reduced landfill disposal associated with Cr bricks, a specially controlled industrial waste material.
For waste not sent to landfills, like Social Recycling B and Corporate Recycling C, we work to reduce emissions, select materials for reuse, and repurpose waste for thermal energy through incineration.
In fiscal 2023, we emitted 1,370 tons of plastic waste from our Japanese plants. Of this, 802 tons were classified as Corporate Recycling C and Landfill Waste D, while 568 tons were reused as Social Recycling B.
We will continue these waste reduction efforts across our overseas plants.
Normal Waste (Landfill Waste D) per Total Weight of Products Sold
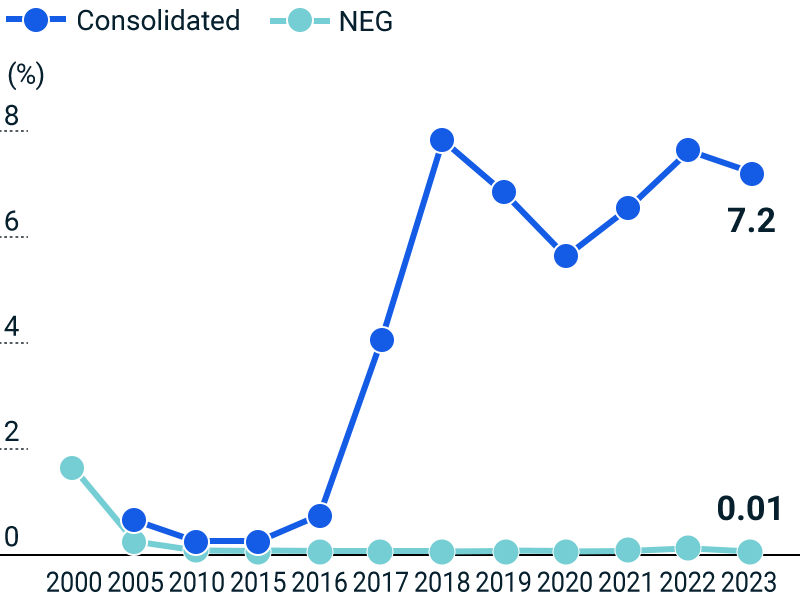
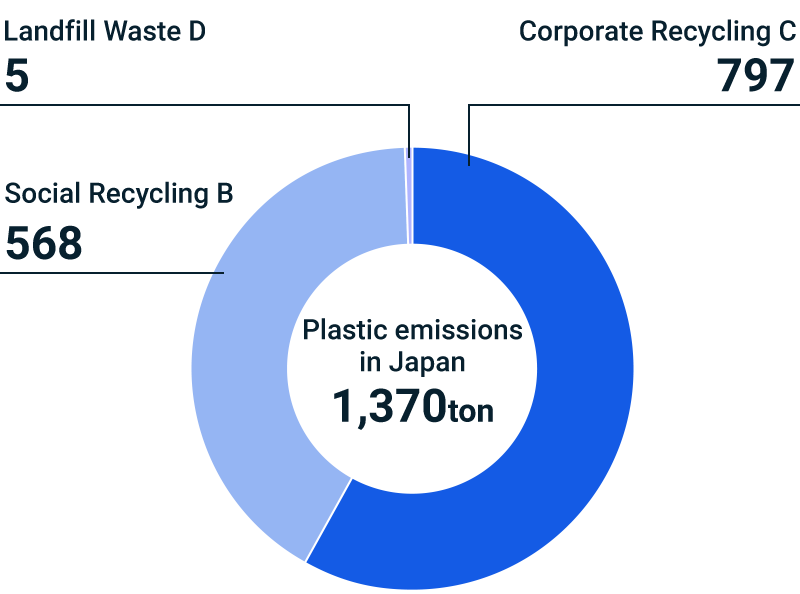
Water Reduction
Since launching our water business plan in fiscal 2003, we have focused on making efficient use of water resources. We see water management as a reflection of our manufacturing sophistication. By managing our water usage, we gain a clearer understanding of glass manufacturing processes, allowing us to improve process technology and equipment.
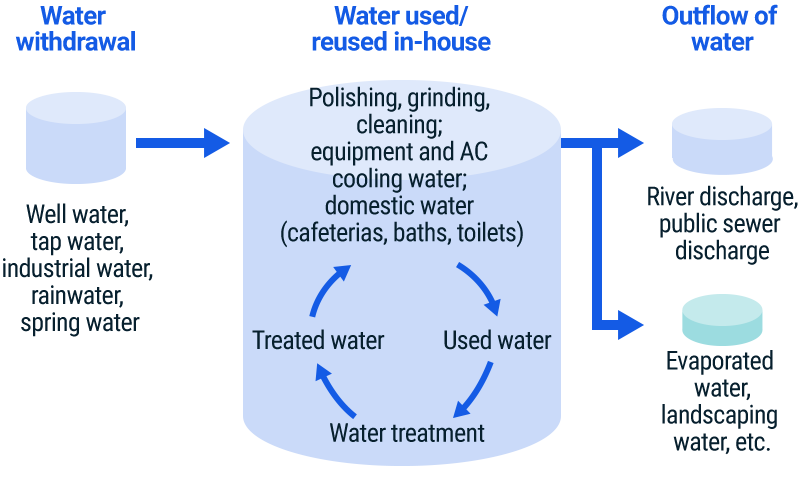
The graphs illustrate the changes over time in water withdrawal and wastewater per total weight of products sold.
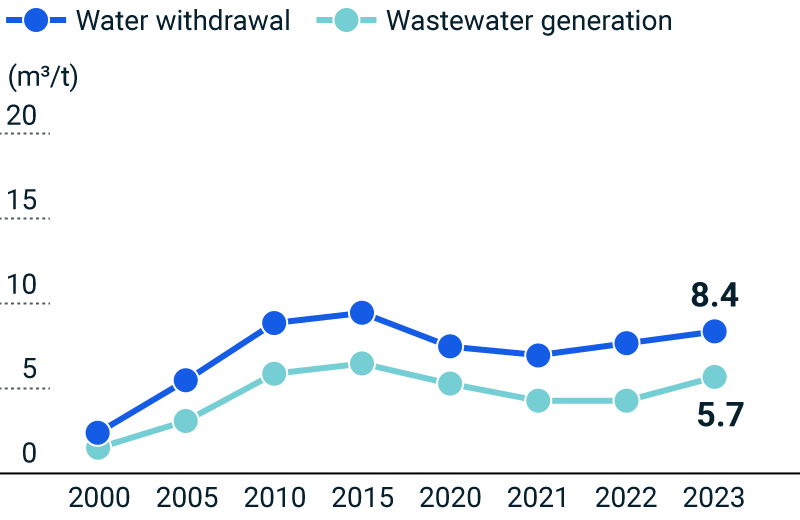
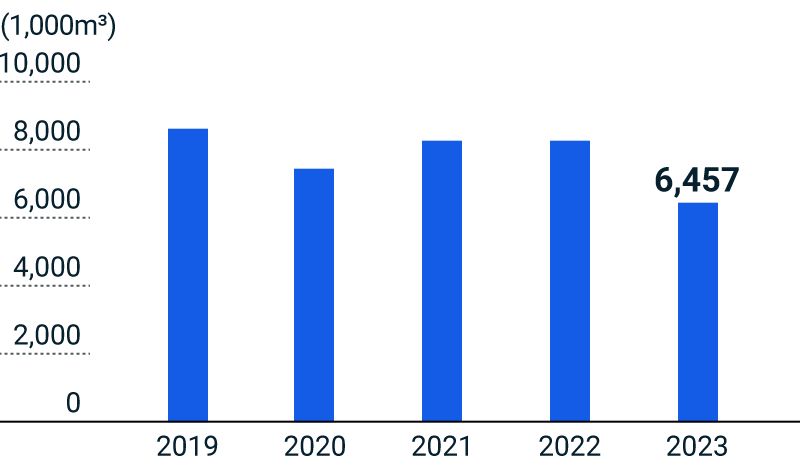
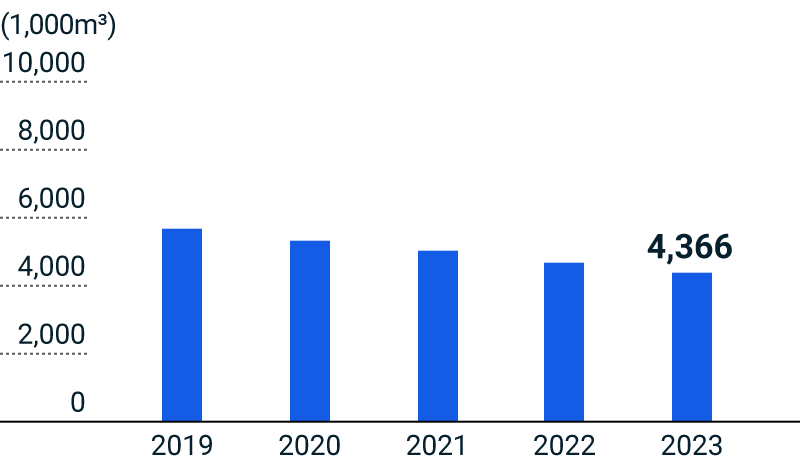
Since 2014, we have seen a steady decline in water intensity within our displays business, a result of our management's commitment to enhancing utilization efficiency. This improvement follows an initial increase in water intensity in 2004, attributed to our transition from CRTs to LCDs.
To further reduce water withdrawal volumes, we actively promote the reuse of water in high-volume stages, such as cooling during melting and forming, as well as cleaning during processing. Additionally, we are minimizing water withdrawal and wastewater generation for other applications by implementing cascading (downcycling) strategies tailored to the specific purposes and quality requirements of water use, alongside recycling water through purification methods.
Initiatives to Protect the Global Environment
As part of our commitment to sustainability and protecting the global environment, we implement initiatives to conserve biodiversity while supplying and developing eco-friendly products that promote energy conservation and generation.
Nippon Electric Glass Signs Its First VPPA for Solar Power
In 2023, NEG signed its first Virtual Power Purchase Agreement (VPPA) with a renewable energy generation operator. Made possible in Japan 2022, a VPPA is a new model for virtually procuring the environmental value of renewable electricity generated off-site. This agreement is expected to reduce CO₂ emissions by approximately 770 tons per year. Moving forward, we will continue to promote initiatives aimed at achieving carbon neutrality.
● Power Plant Locations: Five sites across Mie Prefecture, including Matsusaka City
● Power Generation Start: March 2024
● Contract Duration: 20 years
Green Factory Certification
Our Chinese subsidiary, Electric Glass (Xiamen) Co., Ltd., has been awarded Green Factory certification by the Chinese government, which recognizes it as a model factory that reduces environmental impact while maintaining productivity. The Green Factory certification program was established by the Chinese government in 2015 to promote environmentally friendly manufacturing models. Electric Glass (Xiamen) has achieved provincial-level certification for its efforts to enhance production efficiency and lower carbon emissions in its energy consumption. The NEG Group, as a whole, will continue striving toward sustainable manufacturing.
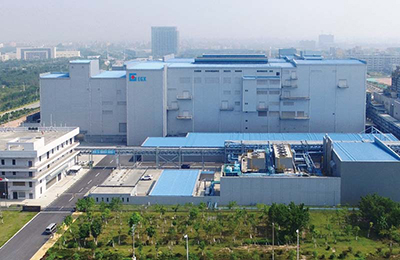