Glass Paste
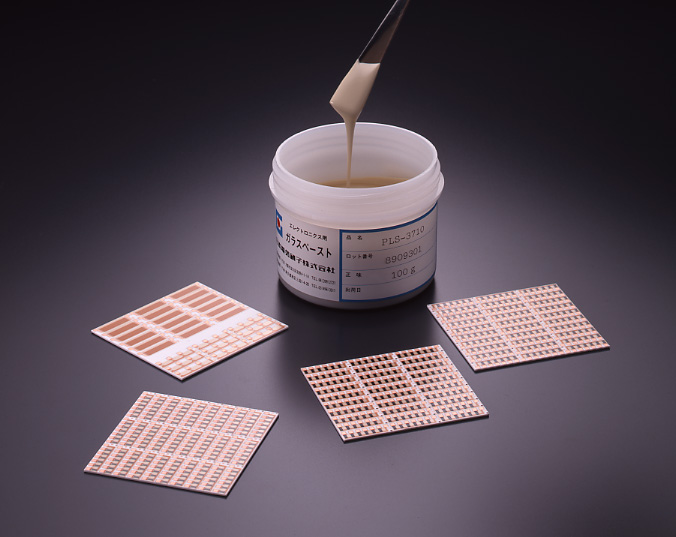
Glass paste is a uniform dispersion of powdered glass on a vehicle. We offer comprehensive guidance to help you choose the optimal glass type, viscosity, and other properties tailored to your specific needs.
・ Choose the glass best suited for your application from a wide range of options.
・ glass pastes can be applied directly in your coating process.
・ PLS-3123 and PLS-3124: These pastes form overcoat films with excellent laser trimming properties and moisture resistance.
・ PLS-3150B1: This paste offers superior acid resistance and maintains its color after electrode plating.
For guidance on glass selection, viscosity adjustments, or other technical specifications, please contact us.
Properties
Refer to the chart below for examples. Lead-free products are available upon request.
For guidance on glass selection, viscosity adjustments, or other technical specifications, please contact us.
Applications | Ag/Pd wiring and Ag/Pt wiring for hybrid IC | For chip resistors | For chip resistors | Various ceramics | ||
---|---|---|---|---|---|---|
Overcoat | Secondary coat | Overcoat | Overcoating, sealing, and bonding | |||
Glass code | PLS-3123 | PLS-3124 | PLS-3150B1 | PLS-3901 | PLS-3143 | |
Firing conditions Peak hold time |
Firing at 510°C for 10 minutes in air | Firing at 580–620°C for 10 minutes in air | Firing at 610°C for 10 minutes in air | Firing at 850°C or higher for 10 minutes in air | ||
Screen | 165-325 mesh | |||||
Post-firing film thickness | μm | 10-50 | ||||
Color tone | Green | Black | White | White (after firing, semi-transparent) | ||
Paste viscosity | Pa・s | 90 | 180 | 230 | 110 | 150 |
Coefficient of thermal expansion | ×10-7/K | 67 | 70 | 67(30-300℃) | 66 | |
Softening point | ℃ | 530 | 585 | 590 | 840 | |
Diluent | Terpineol | |||||
Features | Forms glass films with high hermeticity and moisture resistance. Widely used in automotive hybrid ICs. |
High viscosity type of PLS-3123 |
Good acid resistance | |||
Type | Lead-containing | Lead-free |
For guidance on glass selection, viscosity adjustments, or other technical specifications, please contact us.
Example Usage
-
Printing
Apply the paste onto the substrate using the screen printing method. Adjust the printing conditions to meet the requirements of your specific application. -
Leveling
To ensure a smooth surface, allow the printed paste to level at room temperature for 5–10 minutes after printing. -
Drying
Dry the paste at 100–150°C for 10–15 minutes. -
Firing
Use a belt furnace or batch furnace for firing. To decompose organic components in the dried coating, a heating rate of 20–50°C per minute is recommended. To prevent damage to the substrate or glass film from thermal shock, cool at a rate of 20–50°C per minute.
Precautions for Use
-
Store the paste in a cool, dark place at or below 25°C, avoiding direct sunlight.
-
If the paste has been stored for an extended period, stir thoroughly with a stainless steel spatula or similar tool to ensure it is well-mixed and uniform.
-
Adjust viscosity if necessary.
-
Ensure adequate ventilation when using the paste, and avoid prolonged inhalation of solvent vapors.
-
If the paste comes into contact with your skin, wipe it off immediately.
Need More Details? Connect with Us!
Related Products
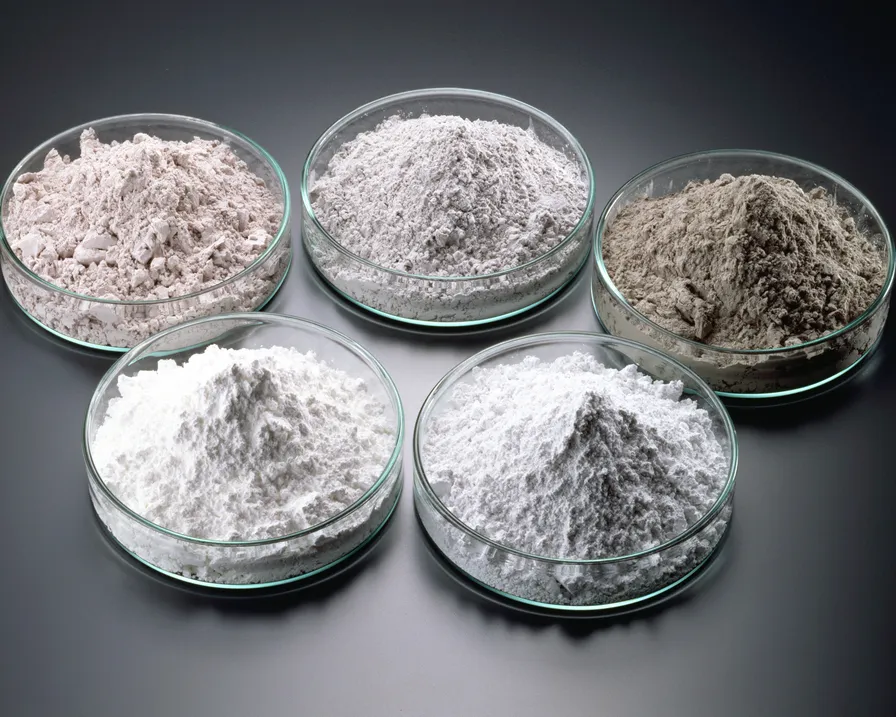
Low Temperature Sealing Glass
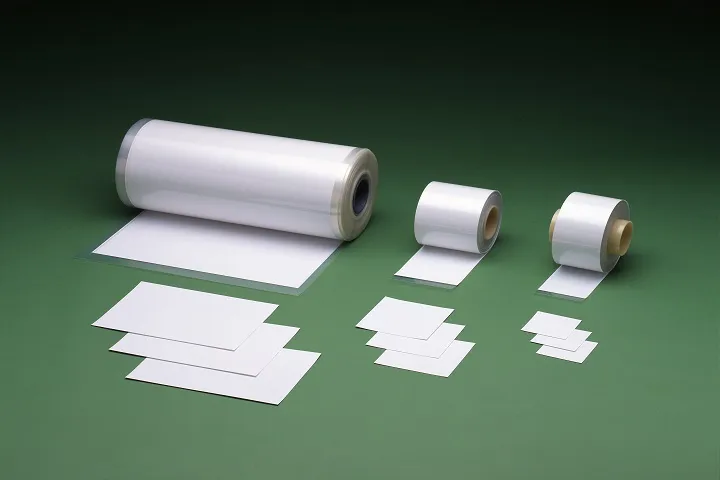
Composite Powder for Low Temperature Cofired Ceramics
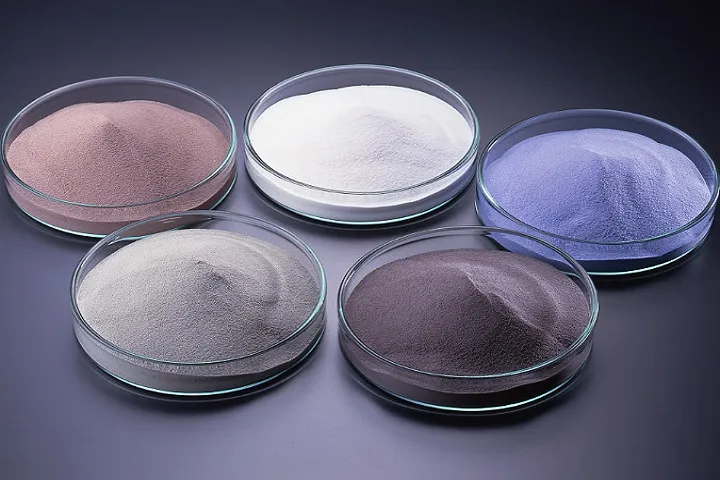
Granulated Glass for Metal Packages
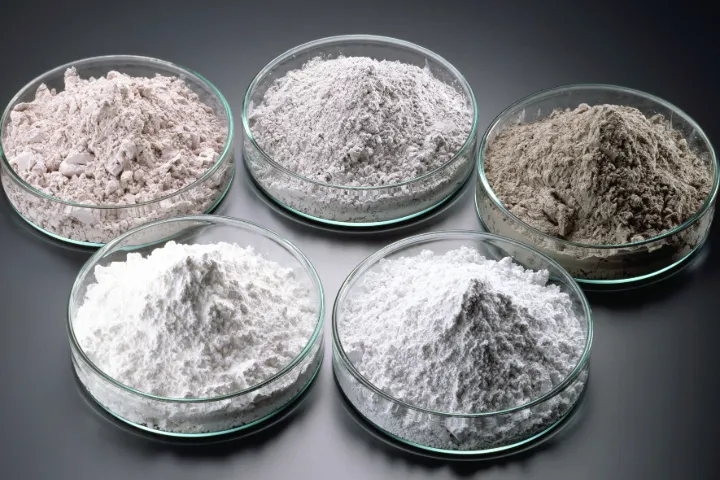
Powder Glass for Coating, Binding, and Sealing
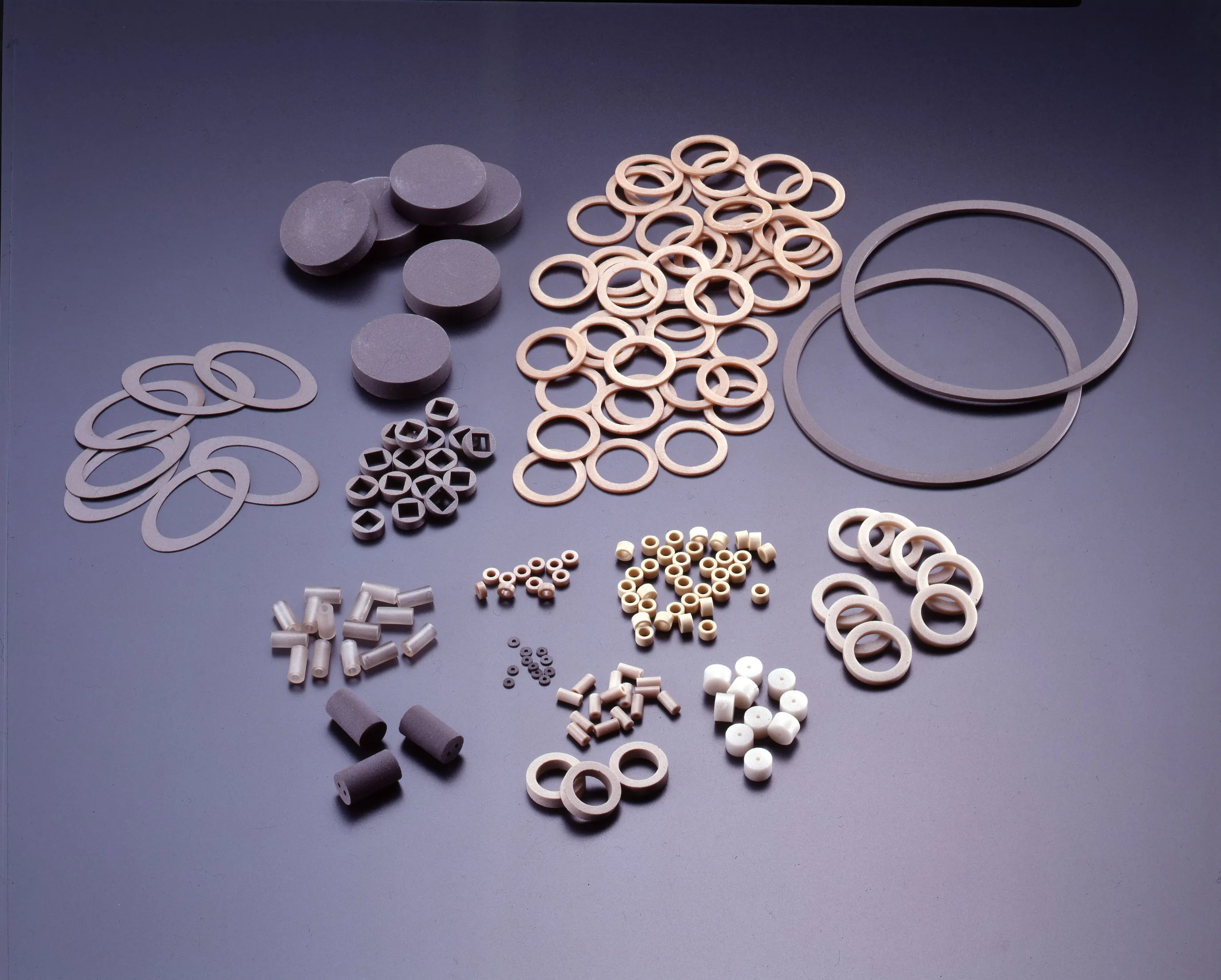
Tablet
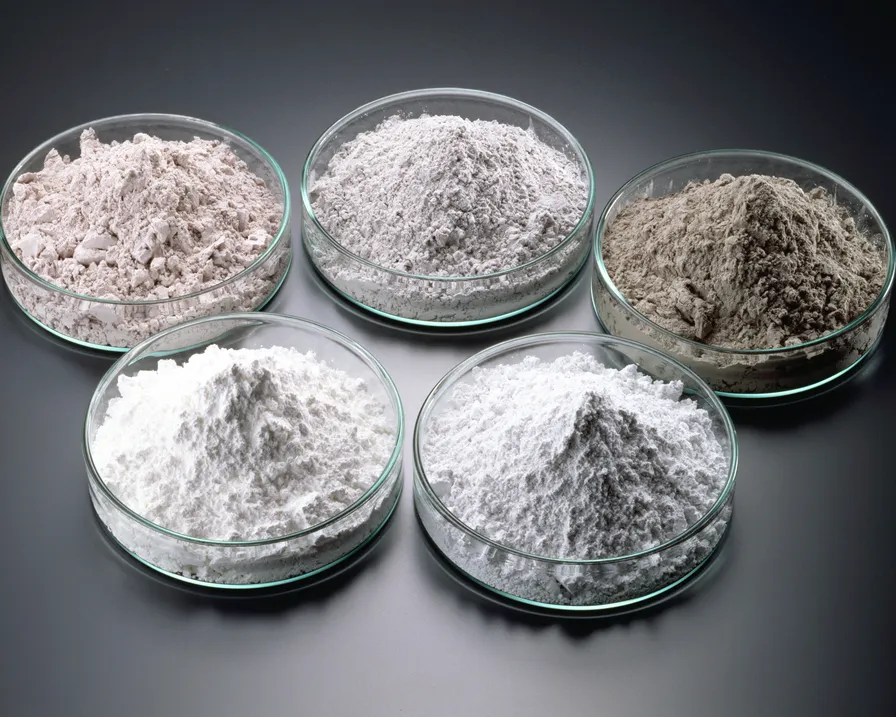
Passivation Glass
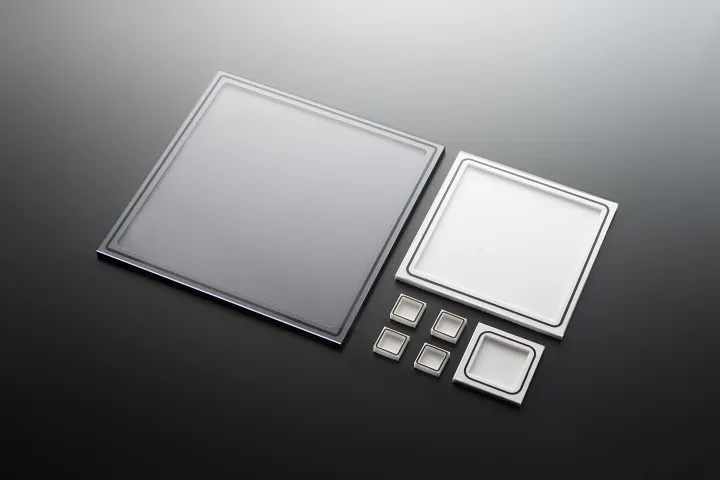