Core Technologies
The NEG Group’s Manufacturing Approach
To meet society’s ever-changing needs, we focus on research and development using cutting-edge technologies to create world-class products. Our ideal manufacturing process is a continuous cycle: efficiently producing high-functionality glass to the highest quality standards, supplying it, and integrating market feedback into our research and development efforts.
Core Technologies
Material Design
Glass can incorporate elements from nearly any material. By adjusting its composition, we can create superior glass that balances various properties to achieve optimal results. This involves a cycle of repeated composition modification, test melting, processing, and evaluation, ensuring that our glass meets all required performance criteria.
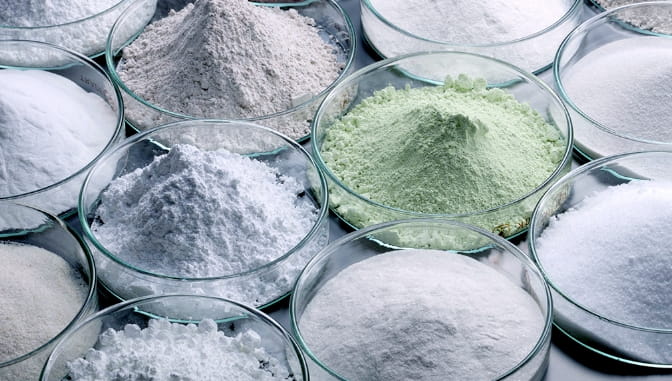
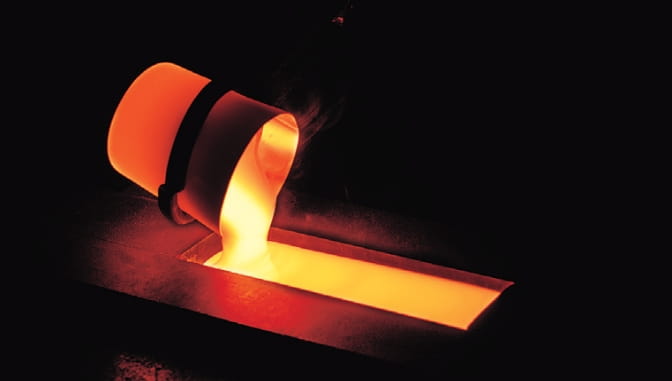
Thermal | Heat resistance, fire protection, low-temperature sealing |
Optical | Light absorption, wavelength conversion, optical thin film |
Electromagnetic | Insulation, dielectric, conducting film |
Mechanical | High-strength through chemical strengthening or crystallization |
Chemical | Acid and alkali resistance, controlled chemical release |
Other | Gas barrier, strengthening plastics and cement |
- Glass with a wide range of coefficients of thermal expansion
- Heat-resistant glass with adjusted strain and softening points
- Glass with controlled transmittance across a broad spectrum of light wavelengths
-
Controlled chemical durability glass
-
Glass with controlled dielectric properties
Evaluation Technology
Our state-of-the-art evaluation technologies are vital to developing high-performance special glass. Our advanced analytical equipment includes X-rays, synchrotron radiation, lasers, magnetic field devices, and trace analysis instruments, which allow us to analyze glass at the parts per billion (ppb) level. We go beyond glass analysis, even visualizing interfaces between materials in glass-based composite devices. These evaluation technologies help us gain insights into the fundamental principles of glass, expanding its limitless potential.
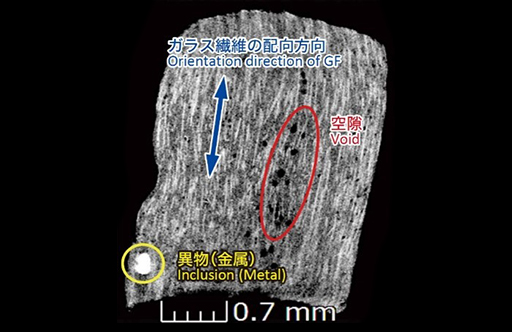
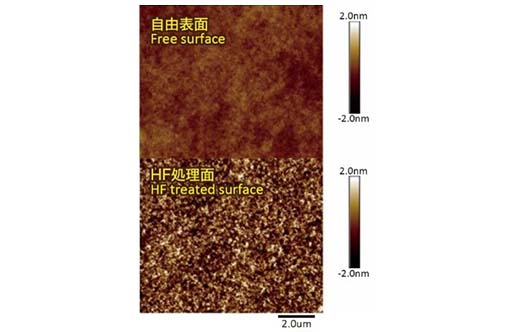
Chemical Analysis
We ensure the quality of our special glass by strictly controlling major and trace elements. Our precise trace analysis techniques allow us to identify specific hazardous substances and adhere to the RoHS Directive. At the same time, our fast and accurate composition analysis guarantees glass meets the high standards of international certification ISO/IEC 17025.
Physical Properties
To meet the design requirements for our special glass products, we measure a comprehensive range of glass properties. These include optical properties such as transmittance and refractive index; thermal properties like strain point, annealing point, softening point, and coefficients of thermal expansion; mechanical properties including elastic modulus, hardness, and density; electrical properties such as dielectric constant and electrical resistivity; and chemical properties like water resistance and weatherability. Additionally, our custom-designed evaluation tools are capable of measuring glass under specific high-temperature conditions.
Glass Defect Analysis
By analyzing defects down to microscopic levels and trace components, we not only identify foreign materials but also pinpoint the mechanisms behind their occurrence. This process enables us to uphold high quality standards and improve manufacturing yields.
Surface/Interface Analysis
The chemical state of glass surfaces greatly influences its properties. Proper understanding of surface composition, structure, and condition is essential, especially for surface analysis of coated devices. We apply a range of evaluation technologies—from optical methods for surfaces to mechanical methods using stylus instruments, even observing structure with electron microscopes—to ensure accuracy at every step.
Process Technology
NEG's process technologies cover the full spectrum of glass production, from melting to forming and processing—all adapted to the unique characteristics and shapes of each type of glass. These processes are constantly refined to meet increasing demands for functionality and precision in our products.
Melting
Creating high-quality glass requires precise furnace control technologies, which we leverage to optimize furnace design and glass melting processes. Our advanced and sensitive furnace operations utilize combustion control, thermal management, and other techniques that enable us to produce high-performance glass while minimizing environmental impact.
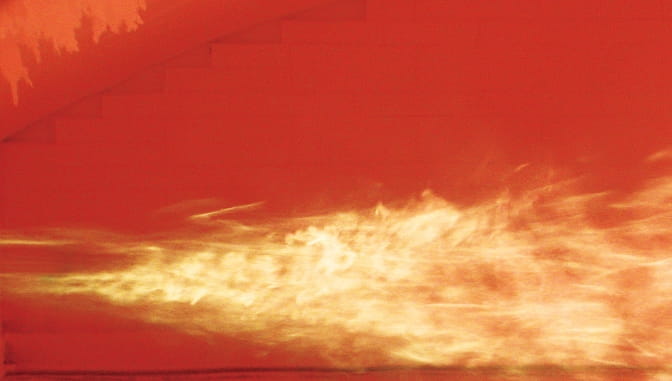
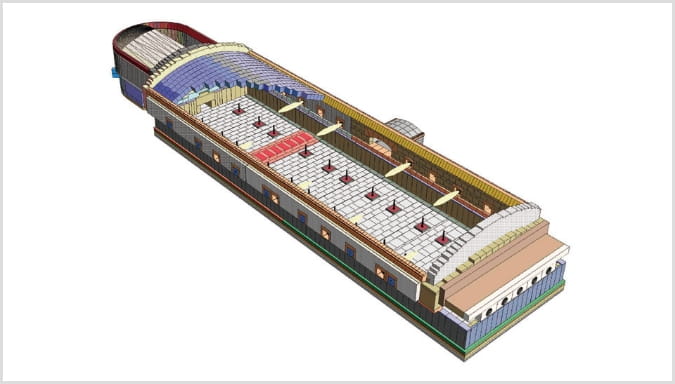
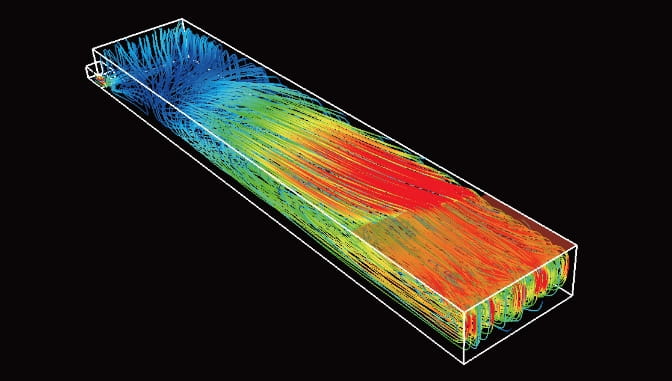
Combustion | Melts glass using the heat generated from the efficient burning of fuels like natural gas and oxygen. | ||
Furnace monitoring | Real-time monitoring of furnace conditions and processes for safer, more efficient production | ||
Electric melting | Energy-efficient glass melting that directly heats molten glass by passing electric currents through inserted electrodes | ||
Computational Fluid Dynamics(CFD) | Visualizes molten glass flow and temperature to optimize furnace design and productivity | ||
Exhaust gas treatment | High-level removal of harmful substances (SOx, dust) from melting furnace exhaust emissions |
-
Glass Engineering
All of our glass manufacturing processes have been painstakingly engineered over the course of many years to reduce CO2 emissions at every stage.
Forming
We apply various forming technologies to achieve dimensional precision and fulfill production requirements. By applying the optimal forming process to each product, we gain exceptional accuracy and efficiency.
Tubing | Achieves a uniform thickness and smooth surface in forming tubular glass from small to large diameter tubes | ||
Overflow | Creates large glass plates with ultra-smooth, nanometer-level surfaces on both sides since both surfaces remain free during forming | ||
Blowing | Forms thin-walled glass by only making contact with the external mold, allowing the solidification layer to thin during cooling. | ||
Pressing | Produces thick, dimensionally precise shapes with improved productivity | ||
Rolling | Rollers on both sides rapidly cool and form glass prone to thickness and crystal precipitation | ||
Float | Method of forming high-flatness plate glass, enabling mass production of wide plates | ||
Spinning | Allows mass production of glass fibers by bundling hundreds to thousands of glass threads with diameters ranging from a few μm to tens of μm | ||
Casting | Achieves the production of glass blocks up to 400mm thick |

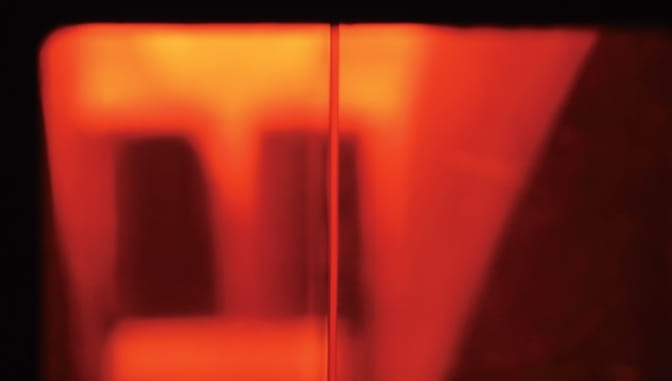
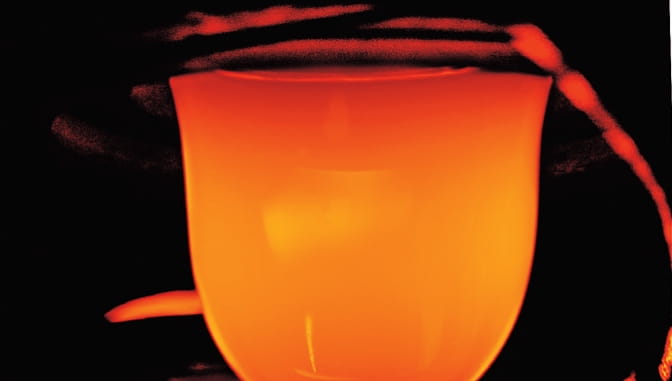
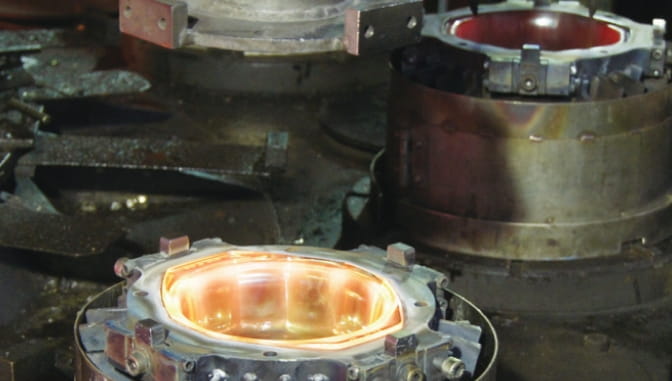
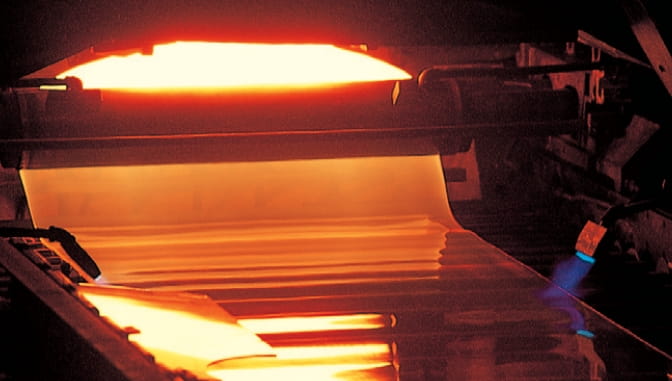
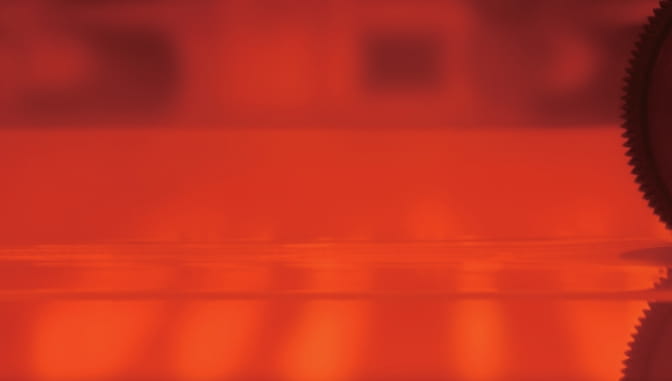
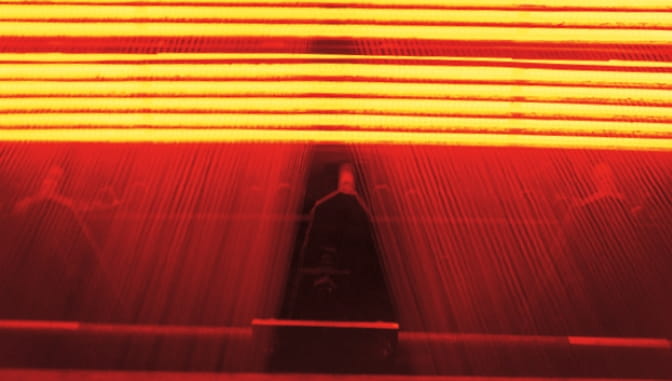
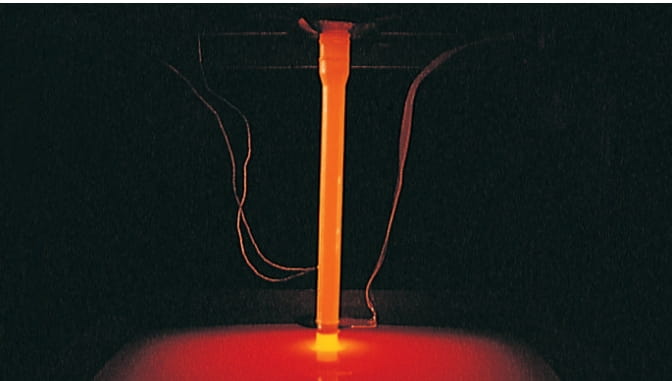
Processing
We employ advanced processing methods, including crystallization, applying thin film coating to glass surfaces, and glass reforming via heat. Our glass can be precision-cut or combined with ceramics or organic materials. This allows us to produce even more precise and specialized products, enhancing the shape, function, and properties of glass.
Precision cutting | Enables micro-cutting of high-precision plate glass and composite materials, achieving complex shapes | ||
Precision polishing | Improves strength by reducing surface roughness through grinding and polishing | ||
Firing (Crystallization) | Controls the type, amount, and size of crystals to achieve properties and functions impossible with glass alone, including enhanced heat resistance, thermal shock resistance, and strength | ||
Precision redrawing | Achieves high-precision products by improving dimensional accuracy and reducing size | ||
Compounding | Fulfills unique functional requirements by leveraging the unique characteristics of various materials like adhesives through laminating glass and resin | ||
Coating and patterning | Adjusts optical performance, conductivity, chemical strength, and mechanical strength to produce high-functionality glass suitable for a wide variety of applications |