History
Since our founding in 1949, NEG has dedicated over half a century to refining glass technology, creating "glass that meets the demands of advancing civilization." As displays have evolved from cathode ray tubes to LCD and OLED technologies, we have developed and supplied special glass that plays a crucial role in various sectors, including ICT, automotive, medical, and lighting, enriching daily life with the power of glass.
With our domestic facilities as the foundation, we have expanded our operations globally to meet the needs of international markets. We are also actively transforming our business structure in response to changing market dynamics. Moving forward, we will continue to refine world-class manufacturing and adapt to global demands.
1944-1959: Establishing the Foundations of NEG
Separating from NEC in 1949, NEG was established with a focus on hand-blown vacuum bulbs and glass tubing. By 1951, we had successfully automated the production of glass tubing using the Danner process. Then in 1956, we transitioned to continuous production of glass tubing using a tank furnace, which solidified glass tubing as the foundation of our business.
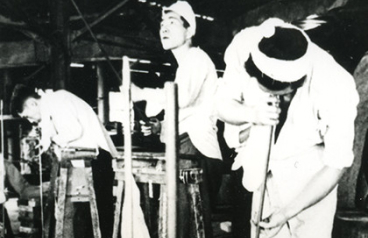
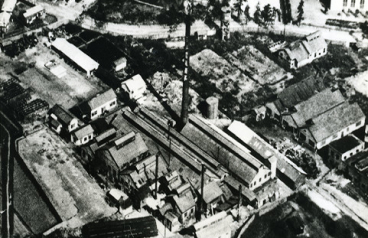
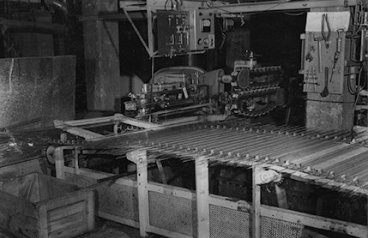
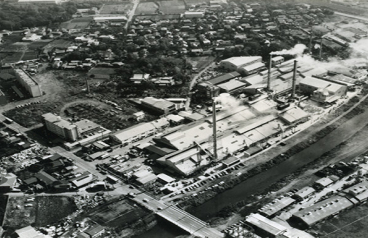
Year | Key Product & Technology Developments | Business Milestones |
||||
---|---|---|---|---|---|---|
1944 | Established in October with investment from NEC Corporation and others Briefly suspended operations after loaning facilities to NEC after World War II |
|||||
1949 | Officially recognized as an independent company on December 1st after separating from NEC |
|||||
1951 | Automated glass tubing production using the Danner process; initiated mass production |
|||||
1956 | Started glass melting production using a large tank furnace Started producing powder glass |
|||||
1958 | Launched production of radiation shielding glass |
|||||
1959 | Started production of glass blocks |
Established Fujisawa Plant |
1960-1989: The Era of CRTs
In 1965, we started producing CRT glass bulbs, marking the start of a growth period aligned with the rise of television and CRT-related businesses in Japan. During that time, we also started producing glass-ceramics, glass blocks, electronic glass materials, and glass fibers, solidifying our position as a leading manufacturer of special glass, with CRT glass becoming one of our core products.
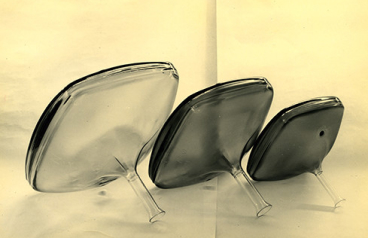
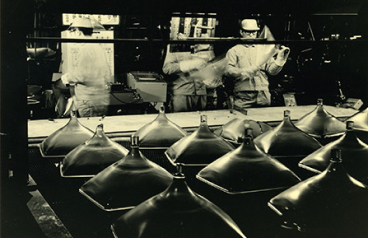
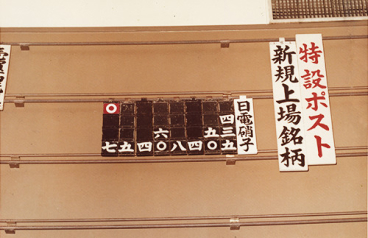

Year | Key Product & Technology Developments | Business Milestones | ||||
1960 | Introduced glass tubing manufacturing technology from Owens-Illinois, Inc. (USA) | |||||
1962 | Developed super heat-resistant glass-ceramic, “Neoceram” | |||||
1963 | Introduced glass CRT manufacturing technology from Owens-Illinois, Inc. (USA) | |||||
1964 | Started production of glass for diodes | Established Shiga-Takatsuki Plant | ||||
1965 | Started production of black-and-white CRT glass | |||||
1968 | Started production of color CRT glass | |||||
1971 | Established Notogawa Plant | |||||
1973 | Developed glass-ceramic building material, “Neopariés” | Company stock listed on the Tokyo Stock Exchange and Osaka Securities Exchange (Second Section) | ||||
1974 | Started production of thin sheet glass for LCDs and heat-resistant glass, “Neorex” | |||||
1976 | Started production of ARG fiber and E-glass fiber | |||||
1977 | Initiated research on glass solidification technologies for high-level radioactive liquid waste, based on a request from the Power Reactor and Nuclear Fuel Development Corporation in Japan | |||||
1980 | Started production of evacuation-type solar tube collectors | |||||
1981 | Started production of glass capillaries for optical connectors | |||||
1983 | Company stock transferred to the First Section of the Tokyo Stock Exchange and Osaka Securities Exchange | |||||
1985 | Started production of extra-large 37-inch CRT glass | |||||
1986 | Started production of D-fiber | |||||
Developed low melting point powder glass for ultra LSl ceramic packages | ||||||
1987 | Pioneered the production of thin sheet glass using the continuous redrawing method | |||||
Started manufacturing alkali-free substrate glass for TFT-LCD panels, cover glass for image sensors, ball lenses for optical communications, and glass for laser diodes | ||||||
1988 | Launched sales of fire-resistant glass-ceramic for fire-rated glass “FireLite” | Launched CRT glass operations in the US through a joint venture, which became a wholly-owned subsidiary in 1993 | ||||
1989 | Developed ball lens unit for optical communications | Made the US representative office a sales subsidiary | ||||
Established Precision Glass Center |
1990-1999: Overseas Expansion
As we entered the 1990s, NEG started to establish a global production network in response to the overseas expansion of Japanese CRT manufacturers and increasing global demand. The latter half of the decade saw the emergence of flat panel displays, prompting us to start producing substrate glass.
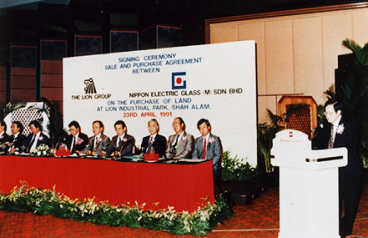
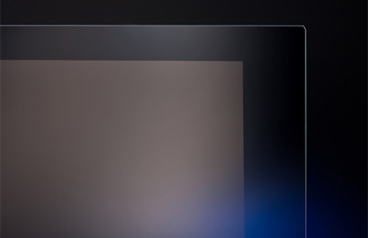
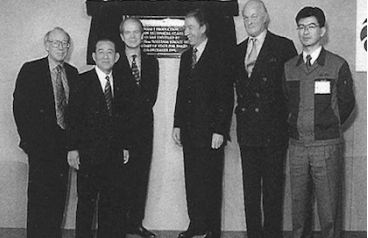
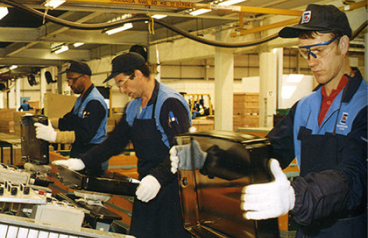
Year | Key Product & Technology Developments | Business Milestones |
---|---|---|
1991 | Established the Wakasa-Kaminaka Plant Started CRT glass operations in Malaysia Codified Environmental Charter |
|
1993 | Introduced oxy-fuel firing systems in melting furnaces | |
1995 | Started production of PDP substrate glass and H-fiber | Started CRT glass operations in the EU (UK) |
1996 | Started production of glass tubing for LCD backlights |
Started CRT glass operations in Indonesia and glass tubing operations in Malaysia |
1997 | Developed glass-ceramic ferrules for optical connectors | Initiated CRT glass operations in China (Hebei Province) via joint venture |
1998 | Established a recycling system for glass collected from used televisions Started production of PDP substrate glass using the float process |
Started production of glass fiber in Malaysia and CRT glass operations in Mexico |
1999 | Acquired ISO 14001 certification for all plants in Japan | Started heat-resistant glass operations in Malaysia |
2000-2009: The Era of FPDs
To address the rapid growth of the FPD market, we started producing glass substrates for LCDs using the overflow process, focusing on larger and higher-quality glass substrates to meet advanced market requirements.
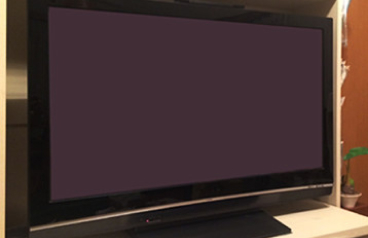
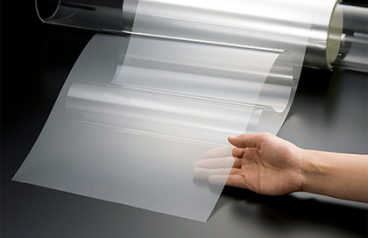
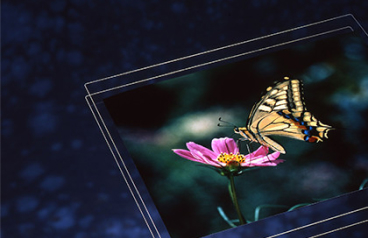
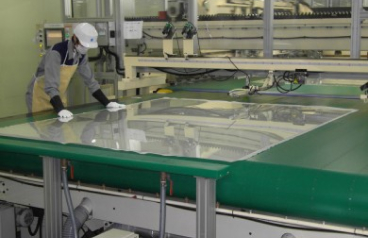
Year | Key Product & Technology Developments | Business Milestones |
---|---|---|
2000 | Started production of LCD substrate glass by the overflow process | Started CRT glass operations in China (Fujian Province) |
2001 | Started production of PDP glass substrates with ITO conductive films using in-line sputtering facilities | |
2002 | Launched sales of D-lens Collimator Components for optical communications | |
2003 | Developed mass production technologies for producing Micro Prisms used in optical devices Developed “CERSAT” negative thermal expansion ceramics for temperature compensation in optical communication devices |
Started processing operations for LCD substrate glass in Korea (Gumi City) |
2004 | Developed “LFX-9” lead-free radiation shielding glass for mammography apparatus | Ended CRT glass production in the US and Mexico Started processing operations for LCD substrate glass in Taiwan |
2005 | Started shipping G7.5 size LCD substrate glass Developed “Pro-GR” gamma-ray shielding glass Created technologies for producing ultra-fine glass fiber Created technologies for direct roll forming for large glass sheets Successfully developed ultra-thin glass sheets at a thickness of 100μm using the overflow process |
Ended CRT glass production in the EU |
2006 | Developed lead-free glass tubing for diodes Acquired ISO 17025 certification for reliable analysis of traces of hazardous impurities exclusively in glass Started shipments of G8 & G8.5 size LCD substrate glass Started CO2 emissions trading, a first between domestic companies |
Started processing operations for LCD substrate glass in Korea (Paju City) via joint venture Ended CRT glass production in Japan Canceled CRT glass joint venture in China (Hebei Province) |
2007 | Successfully developed ultra-thin glass sheet with a thickness of 50μm using the overflow process Developed hemispherical lenses for optical communication devices Developed glass for chemical strengthening |
Concluded a comprehensive university-industry collaboration agreement with the University of Shiga Prefecture Ended CRT glass production in Indonesia Started processing operations for LCD glass substrate in China (Shanghai) via joint venture |
2008 | Developed OA-10G green glass substrate not containing any environmentally hazardous substances Successfully developed ultra-thin glass with a thickness of 50 µm, capable of rolling around a cylinder |
|
2009 | Introduced LX Premium, a new type of radiation shielding glass that does not stain or discolor Developed glass panel with highly efficient UV-blocking coating Launched sales of the world’s largest solar mirror with dielectric film Jointly developed the world’s first thin-film lithium-ion secondary battery on ultra-thin glass, with a thickness of 30µm, with Iwate University Developed extremely thin Glass-ribbon using the redrawing process |
Ended CRT glass production in China |
2010-2014: Building a New Growth Pillar
As the rapid growth in FPD glass sales began to moderate, we shifted our focus to expanding our glass fiber offerings for reinforcing high-performance engineering plastics and glass tubing for pharmaceutical and medical applications. During this period, we also launched several innovative products, including glass for solar cells, cover glass for smartphones, and phosphor-glass composites. Notably, we made significant strides in developing unique products such as Glass-ribbon and glass with a zero coefficient of thermal expansion (CTE).
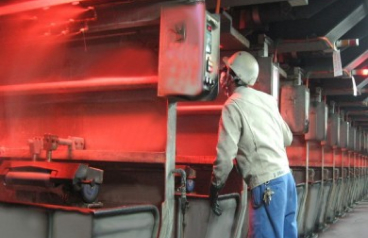
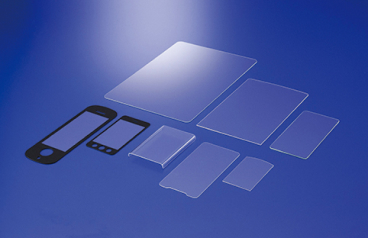

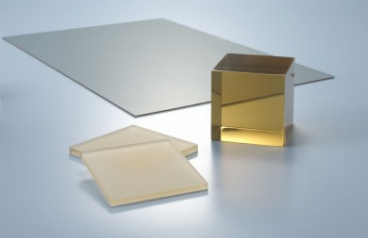
Year | Key Product & Technology Developments | Business Milestones |
---|---|---|
2010 | Initiated shipment of glass substrates for solar cells | |
2011 | Supplied ultra-thin lightweight mirrors for Space Solar Power Systems to the Japan Aerospace Exploration Agency (JAXA) Started mass production of glass for chemical strengthening |
Started production of glass tubing for pharmaceutical use in Malaysia Established P&P Technology Center Takatsuki at Shiga-Takatsuki Plant Established Nippon Electric Glass Europe GmbH in Germany |
2012 | Started sales of “Invisible Glass™” | |
2013 | Developed “ZERØ™” with a coefficient of thermal expansion of zero |
Established P&P Technology Center Otsu at Otsu plant Started melting and forming operations for FPD-related glass in Korea (Paju City) |
2014 | Launched the new brand “Dinorex™” special glass for chemical strengthening Developed “VitroQuartz™”, which has the same coefficient of thermal expansion as quartz |
Started processing operations for FPD-related glass in China (Guangzhou) Established joint venture company, OLED Material Solutions Co., Ltd., at Notogawa Plant Ended melting and forming operations for CRT glass |
2015-Present: Pursuing Further Growth
In 2015, we revised our corporate philosophy and initiated a three-year medium-term business plan in 2016 to drive further growth. To expand our glass fiber business, we acquired a European business in 2016 and an American business from PPG Industries in 2017. As a result, glass fiber has become a key pillar of our operations alongside FPD glass.
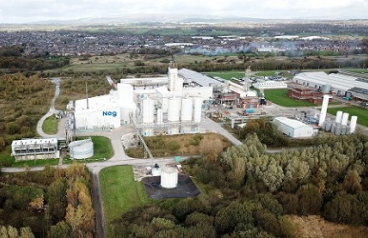
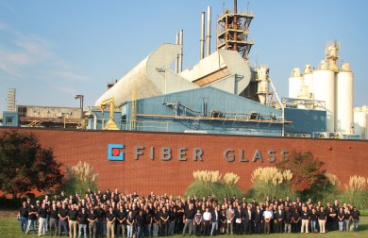
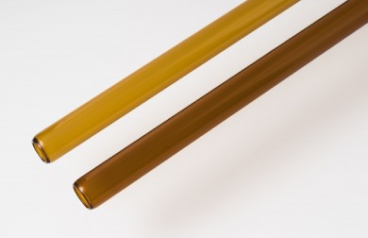
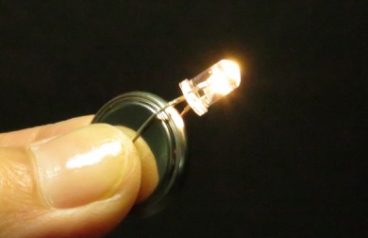
Year | Key Product & Technology Developments | Business Milestones |
---|---|---|
2015 | Developed the world’s thinnest infrared absorbing filter Developed glasses for supporting semiconductor wafers with various CTEs |
Closed Fujisawa plant Started melting and forming operations for FPD-related glass in China (Xiamen) Restructured corporate philosophy system |
2016 | Launched StellaShine™, a new brand of glass-ceramics for cooktop surfaces Developed glass frit for laser-sealing ceramic packages |
Started NEG's first Medium-Term Business Plan EGP2018 Started processing operations for FPD-related glass in China (Nanjing) Acquired European glass fiber business of PPG Industries, Inc. Closed Wakasa-Kaminaka Plant |
2017 | Developed flat glass fiber for reinforcement of thermoplastic resin Developed a new glass tubing material for pharmaceutical and medical use Developed an all-solid-state Na-ion secondary battery using a glass-ceramic cathode |
Acquired glass fiber operations in the U.S from PPG Industries |
2018 | Developed high-efficiency deep UV-transmitting glass Developed an IR absorbing filter with the world’s highest visible light transmittance Developed an optical coating material to realize high contrast for display cover glass Developed the world’s smallest optical isolator for high power fiber lasers using magneto-optical glass |
Purchased carbon offset credits (J-Credit) issued by a forestry association in Shiga Prefecture, to contribute to local environmental conservation banner of NEG Journal: Explore Specialty Glass Trends and Insights |
2019 | Developed infrared lenses using the world’s highest performance infrared transmitting glass Achieved world’s highest performance of substrate glass for smart glass Developed 3D printer paste that enables high-precision ceramic modeling Established mass production technology for micro-ball lenses for 5G with uniform anti-reflection coating Developed lead-free low-melting-point glass frit, enabling sealing at 380℃ |
Established Medium-Term Business Plan, EGP 2021 Certified with top rating (three stars) as a company embracing the Shiga Prefecture Biodiversity Initiative Concluded a naming rights partnership contract with Shiga Prefecture for supporting the Lake Biwa Floating School Program Established a joint-venture on LTCC business |
2020 | Development of glass beads that realize translucency of 3D printed models Achieved practical-level performance of all-solid-state sodium (Na)-ion secondary batteries. (Paper appears in Scientific Reports – Nature) Successful developed world’s thinnest glass as a cover glass for foldable displays Developed 5G-suitable materials for LTCC with the industry’s lowest loss tangent |
|
2021 | Developed and commercialized lid with sealing material for packages of optical devices Developed the world’s first colorless transparent zero-expansion glass-ceramics Developed and commercialized cap lids with the world’s highest light extraction efficiency Developed low-loss LTCC materials for 5G communication Developed the world’s first all-oxide all-solid-state sodium (Na) ion secondary battery |
Concluded “Lake Biwa Carbon Credit” partner agreement with Shiga prefecture afforestation public corporation Donated books to children’s cafeterias in Shiga prefecture Support for the Task Force on Climate-Related Financial Disclosures (TCFD) |
2022 | Succeeded in melting glass with combustion technology using a hydrogen-oxygen burner Developed new products expanding 5G’s wireless communication area Business of jewelry glass infiora™ enters the wedding industry |
Established Medium-Term Business Plan, EGP 2026 Agreed to establish an endowed chair in basic science of glass with Kyoto University |
2023 | Developed the world’s first all-glass-ceramic, all-solid-state sodium (Na) ion secondary battery using a glass-ceramic solid electrolyte Lens antenna utilized in self-driving bus convoy demonstration |
Started operation of a mega solar system at Shiga-Takatsuki Plant Signed first Virtual Power Purchase Agreement (VPPA) for solar energy |
2024 | Developed “GC Core™”—glass-ceramics core |
Established New Medium-term Business Plan, EGP2026 |